Replacement waste heat boiler for formaldehyde plants
Optimize energy recovery in high-temperature chemical reactions with this advanced waste heat boiler, ideal for transforming excess thermal energy into valuable steam for your process line.
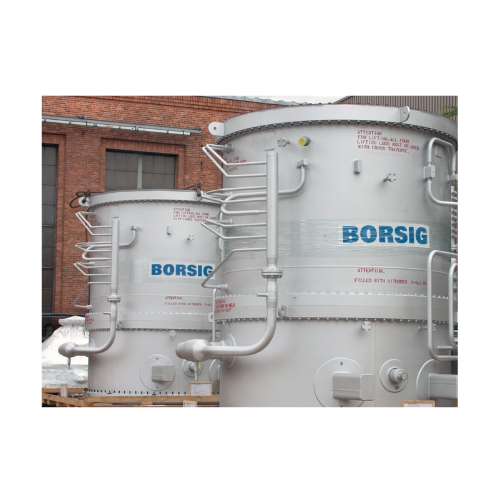
Recovers Heat and Generates Steam for Chemical Processes
BORSIG Process Heat Exchanger GmbH provides sophisticated replacement waste heat boilers tailored for nitric acid, caprolactam, and formaldehyde production. These boilers utilize a forced circulation design, ensuring efficient heat recovery and steam generation by capturing released thermal energy from catalytic processes. Integrating easily into existing lines, they manage up to 500 °C steam temperatures at pressures between 40 and 80 bar. The design supports continuous operation, optimizing energy use, and ensuring sustainable production processes. Available in different material options for corrosion resistance, they offer seamless compliance with international standards. Featuring an integrated cooling system, these boilers maintain operational efficiency while facilitating easy maintenance with an available CIP system. Custom engineering support is offered to meet specific production requirements, enhancing plant efficiency and reliability.
Benefits
- Enhances energy efficiency by recovering and utilizing waste heat, leading to lower operational costs.
- Supports high-pressure operations, maximizing steam output for improved production capacity.
- Robust material options ensure durability in corrosive environments, reducing maintenance frequency.
- Facilitates seamless integration into existing production lines, minimizing installation downtime.
- Contributes to sustainable production practices by optimizing thermal energy recovery.
- Applications
- Nitric acid, Caprolactam, Formaldehyde
- End products
- Pentaerythritol, Urea-formaldehyde resins, Adipic acid, Phthalic anhydride, Melamine formaldehyde resins, Nylon-6, Hexamine
- Steps before
- Feed gas preparation, Catalyst bed setup, Ammonia combustion, Methanol dehydration
- Steps after
- Steam superheating, Gas cooling, Steam delivery to process
- Input ingredients
- ammonia, methanol, water, air
- Output ingredients
- nitric oxides, formaldehyde, superheated steam, saturated steam
- Market info
- BORSIG is known for its expertise in manufacturing high-quality industrial engineered-to-order (ETO) equipment, including pressure vessels, heat exchangers, and compressors, with a strong reputation for engineering excellence and reliability in the petrochemical and chemical industries.
- Operating Temperature
- 600–900 °C
- Operating Pressure
- 5 bar (500 kPa)
- Steam Production Temperature
- 150–500 °C
- Steam Production Pressure
- 20–80 bar (2, 000–8, 000 kPa)
- Design Type
- Forced circulation
- Boiler Type
- Fire-tube boiler
- Element Type
- Flat spiral elements / Meander coil elements
- Heat recovery process
- Waste heat recovery using catalytic oxy-dehydration
- Pressure levels
- 5 bar (500 kPa) to 80 bar (8000 kPa)
- Integrated heat recovery
- Integrated waste heat boilers in process reactors
- Temperature control
- Superheated steam temperatures up to 500 °C
- Steam generation
- Saturated and superheated steam production
- Operation type
- Batch or continuous operation possible
- Corrosive resistance (e.g. acids)
- Yes
- Cleanability
- Yes
- Durability under high temperatures (up to 900°C)
- Yes
- Resistance to catalytic reactions (e.g.,platinum gauze)
- Yes
- Thermal conductivity for efficient heat transfer
- Yes
- Suitable processes
- Nitric acid, formaldehyde, caprolactam production
- Valves
- Control ball / Isolation, emergency shut-off