How to make a more effective fuel: black pellets
Torrefaction is a thermal process where biomass is heated in the absence of oxygen at atmospheric pressure to create a coal-like material, in the shape of black pellets (also known as torrefied pellets). It creates a fuel that has a 30 percent higher energy density, compared to regular white wood pellets, which improves heating value.
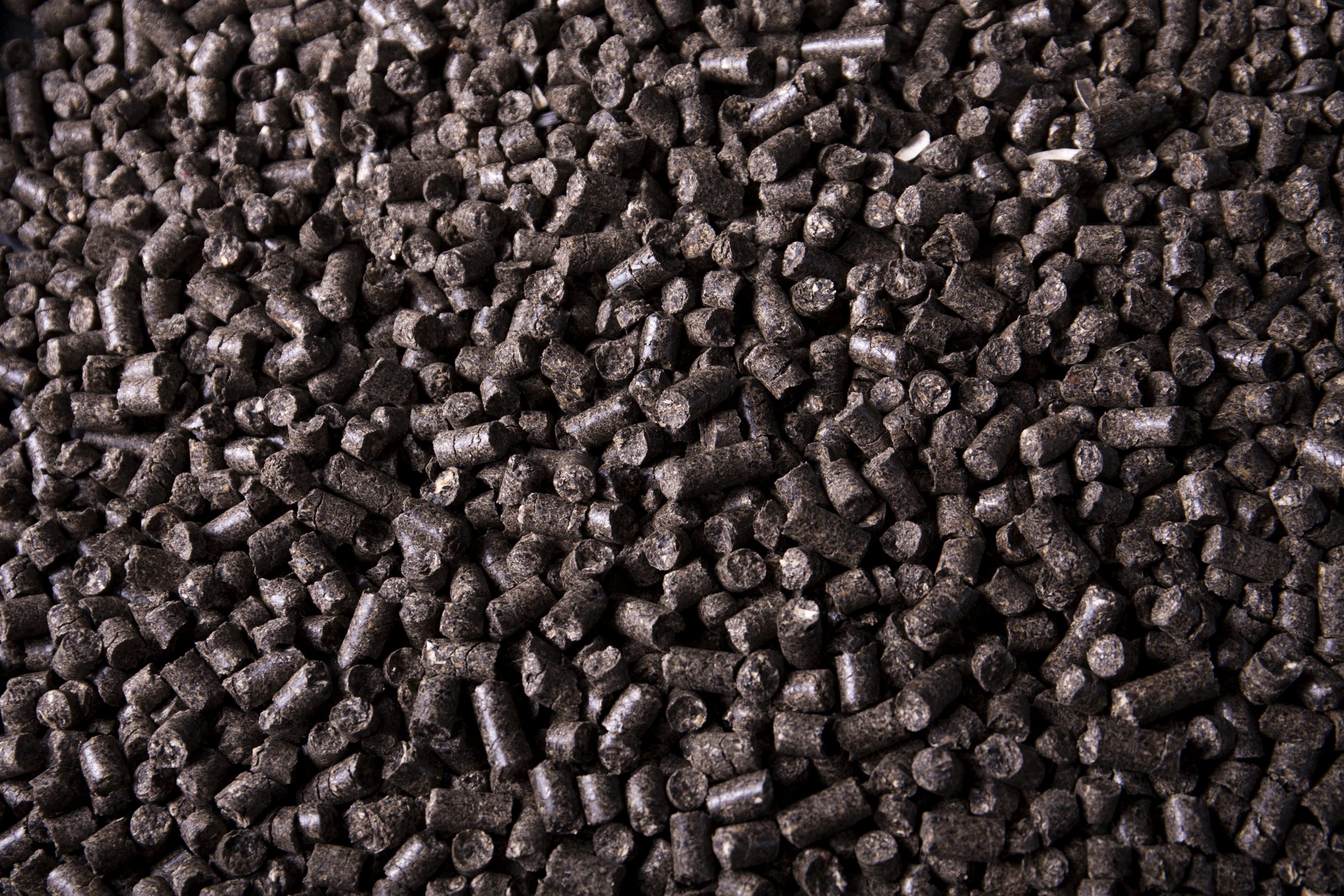
What are black pellets used for?
Black pellets are used to replace natural gas or fossil coal in industrial boilers. Also, torrefied biomass is produced large-scale to cater to thermal power generators and gasification power generators for co-firing purposes because of the high heat value. Other industrial process heating applications can include the use of these pellets for district heating networks. The demand for these pellets is not growing as fast as originally expected considering the gains in fuel efficiency for these renewables. Half the production capacity worldwide is in the hands of a company in the US that produces 33 tonnes black pellets per hour. High initial investment in a torrefaction reactor turned out to a barrier to start up processing these more effective pellets, especially compared to the low investment needed to buy white pellets as a renewable fuel source.
Industrial processing of black pellets
To produce torrefied pellets, biomass such as wood or straw are delivered to a torrefaction site like that of Blackwood Technology shown in the video below. The first step in the process is to dry the biomass from a 50 percent moisture content to less than 15 percent. The pre-dried biomass is then fed to a torrefaction reactor, a sealed environment that is absent of oxygen, where the material is heated to 250/300 degrees Celsius. Here, the volatiles decompose and binding materials in the cell walls break down, changing the properties of the biomass. After torrefaction, the product is cooled down and compacted or pelletised in a pelleting press to create the desired shape of the crushed torrefied biomass.