Every pellet counts! Let’s make the plastic recycling process greener
Plastic recycling has a dynamic duo: mechanical and chemical.
Chemical recycling is still in the research stage, aiming to convert plastic into its original building blocks. But our interest lies in mechanical recycling, which involves first sorting, cleaning, and shredding the plastic material and then transforming it into small, uniform pellets.
With no standardized global sorting system in place and a wide range of plastic types, plastic recycling results in a shockingly low recycling rate of only 9%. Fortunately, countries are joining forces to raise this percentage together by establishing uniform recycling guidelines and investing in the development of sorting facilities.
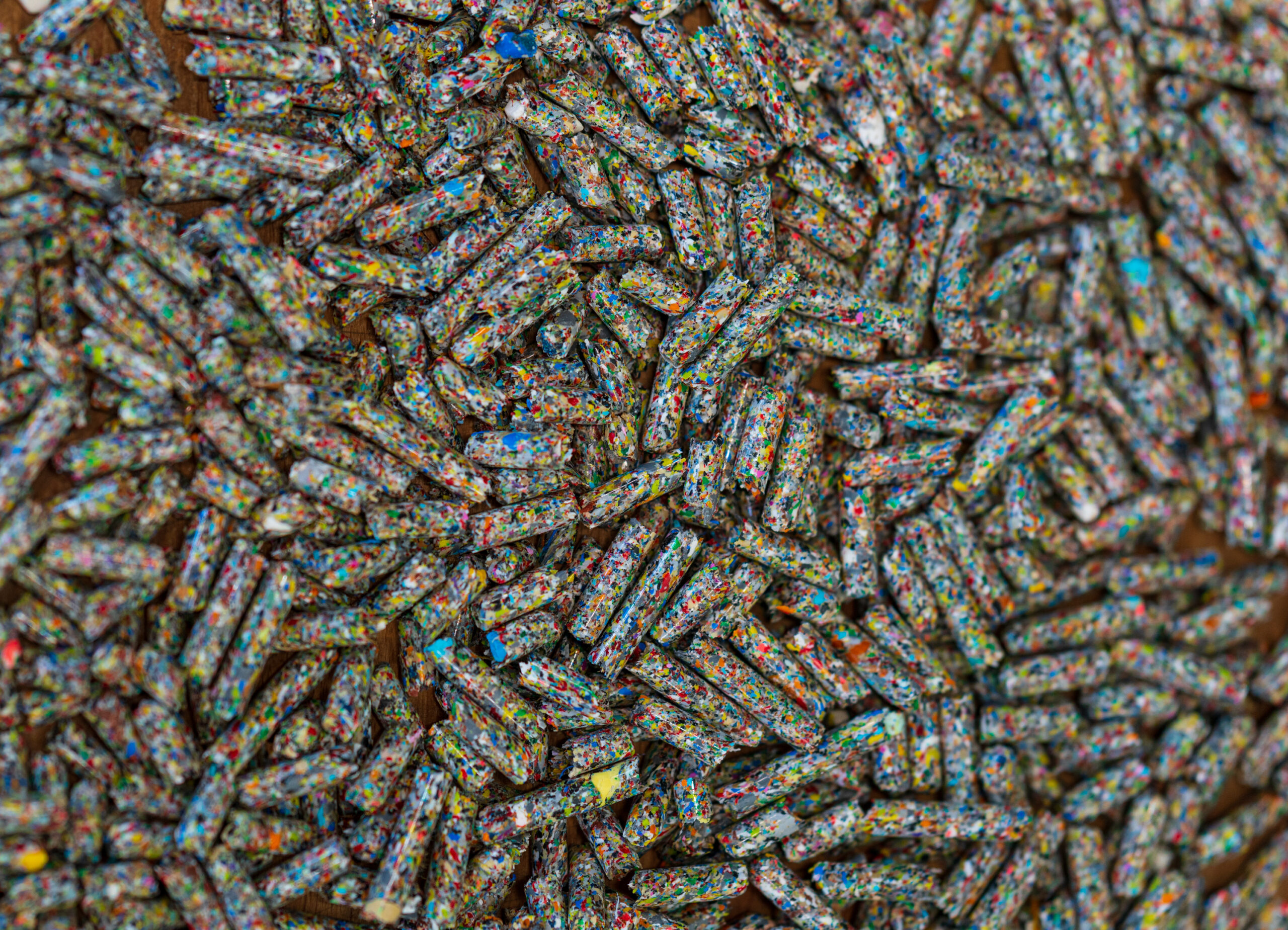
Give plastics a second chance.
We spoke with Timo Muller, from Salmatec, an expert in pelleting technology, about how pelletizing plastics reduces emissions, conserves energy and gives plastics a new life.
But what potential products can be made from recycled pellets?
“Well… you might have even sat on one of them,” replies Timo. “When park benches are not made of wood, there’s a good chance they’re actually made from recycled plastic pellets.”
They typically have a grayish color, but if you look closer, you’ll spot red and yellow colors, which are a testament to the plastic waste that has been reborn.
“Another popular use for pellets involves the production of plastic pillars and various construction materials. The only restriction is that they cannot be used for food packaging due to hygiene concerns,” says Timo.
Why do pelletizing plastics play a crucial role?
“Plastic bottles are typically larger and have a more complex shape compared to pelletized plastic. If you have to melt a plastic bottle, you need more energy to reach the necessary melting point. Pellets just melt faster,” explains Timo.
Pelletizing allows for maintaining the same weight of plastic while significantly reducing its volume saving valuable energy resources.
“Salmatec pellet mill stands out for its energy efficiency in terms of energy consumption per ton of pellet output. This is achieved due to two motors that work in tandem evenly distributing power, minimizing energy waste, and maximizing utilization,” continues Timo.
Before entering the pellet mill, plastic waste needs to be reduced to a particle size of 4 cm. Larger sizes pose a risk of machine plugging and breakdown. The second important factor is moisture.
“Pellet moisture should not exceed 15%, preferably below 10%. It is imperative to check all parameters before entering the pelleting line,” adds Timo.
Recycled plastic pellets are easy to handle, making transportation and storage more efficient while minimizing fuel consumption and our carbon footprint. Moreover, these compact pellets require significantly less space on-site. And who doesn’t always need a little extra space?