Spray Dryer Crack Testing Services
Spray dryers undergo multiple thermal cycles and may develop cracks as the metal becomes fatigued. With traditional visual and dye testing methods, some defects can however be undetected visually. And that happens because cracks formed on the internal surfaces of the vessel may only appear during operation when the temperature is high, and the material expands. But as it cools down, the crack closes and may not be easily identified.
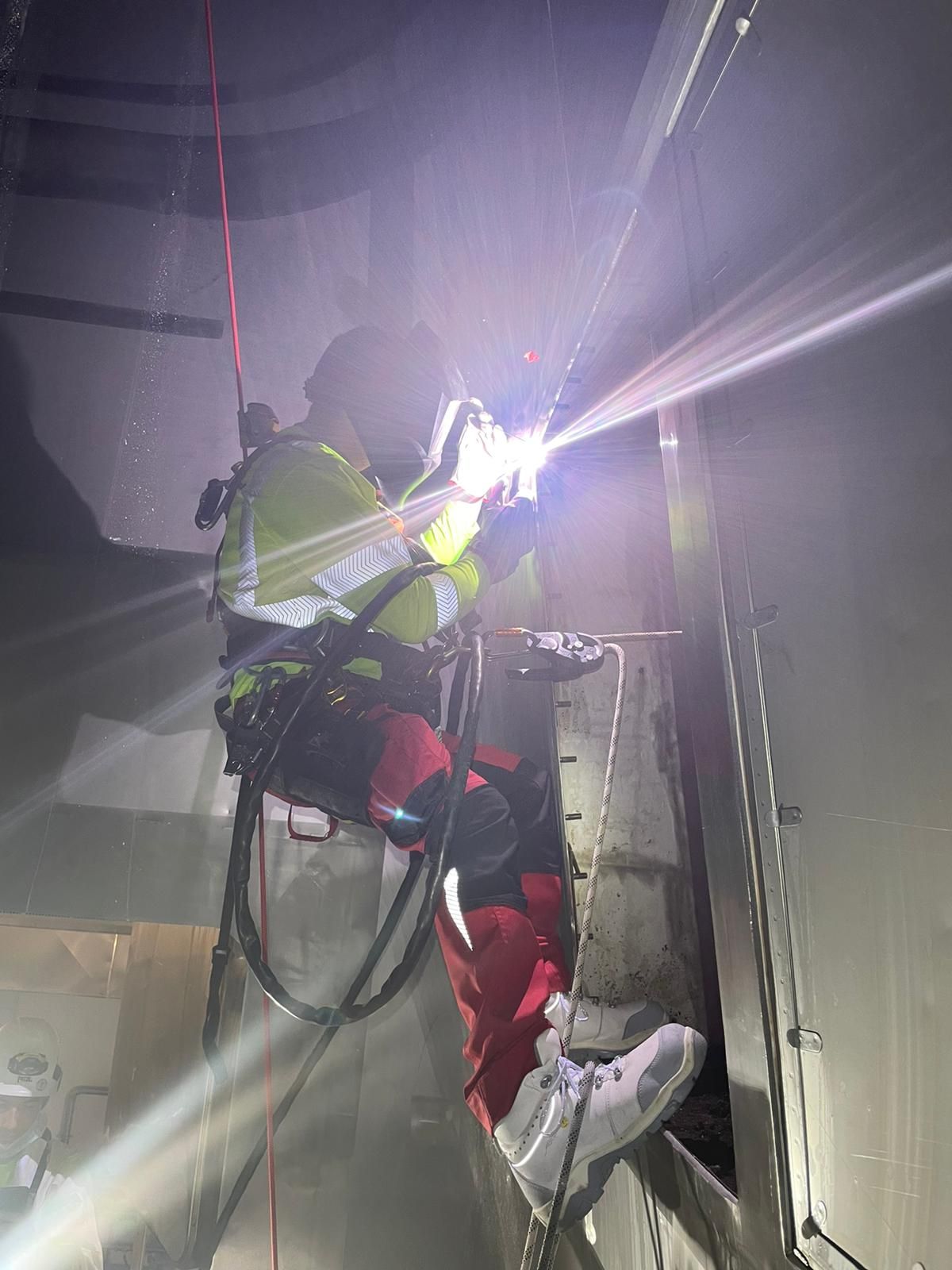
Detecting visual and non-visual defects using an electronic scanning device
Bioscan’s state of the art crack testing services use an electronic scanning device to detect visual and non-visual defects such as cracks, incomplete welds, corrosion cavities, and porosity on spray dryers and other vessels with real-time analysis. These inspection services not only improve safety standards but they also reduce production downtime. Which is why this type of spray drying crack testing is commonly used in both food as well as pharmaceutical industries.
A technician scans the entire vessel surface while the system sends signals for crack detection through audible and visual signals from the control device. The scanner also has multiple sensitivity settings to detect the depth of the defects anywhere from 0.25mm to 5mm. This eliminates the need for liquid penetrant or destructive testing. There is also no need to erect expensive scaffolding to complete the testing of spray drying. The technician is usually suspended via a rope system, lowered down from the access platform.
The entire process can be done in 24 to 48 hours, depending on the size of the dryer and the number of defects. A detailed report is provided for the exact location of defects along with photos of the defects before and after the repair. Bioscan also offers repair services with qualified welders to carry out sanitary repairs during the test duration. Thus, reducing traces and sources of microbial contamination.
Benefits
- Accurate and detailed report of defects
- 24/48-hour downtime
- Environmentally safe testing (No dyes/ chemicals used)
- Cost-effective and less risk of equipment damage (No scaffolding required)
- 100% inspection coverage