Optical sorter for fruit and vegetables
In fresh vegetable and fruit production, product quality is key to ensure a longer shelf life, higher consumer satisfaction, and better wholesale pricing. Traditional sorting involves the use of trained operative, manually removing blemished or damaged items from a conveyor system. If you need to reduce your costs and improve the quality of your products then moving to an automated sorting solution can bring huge benefits.
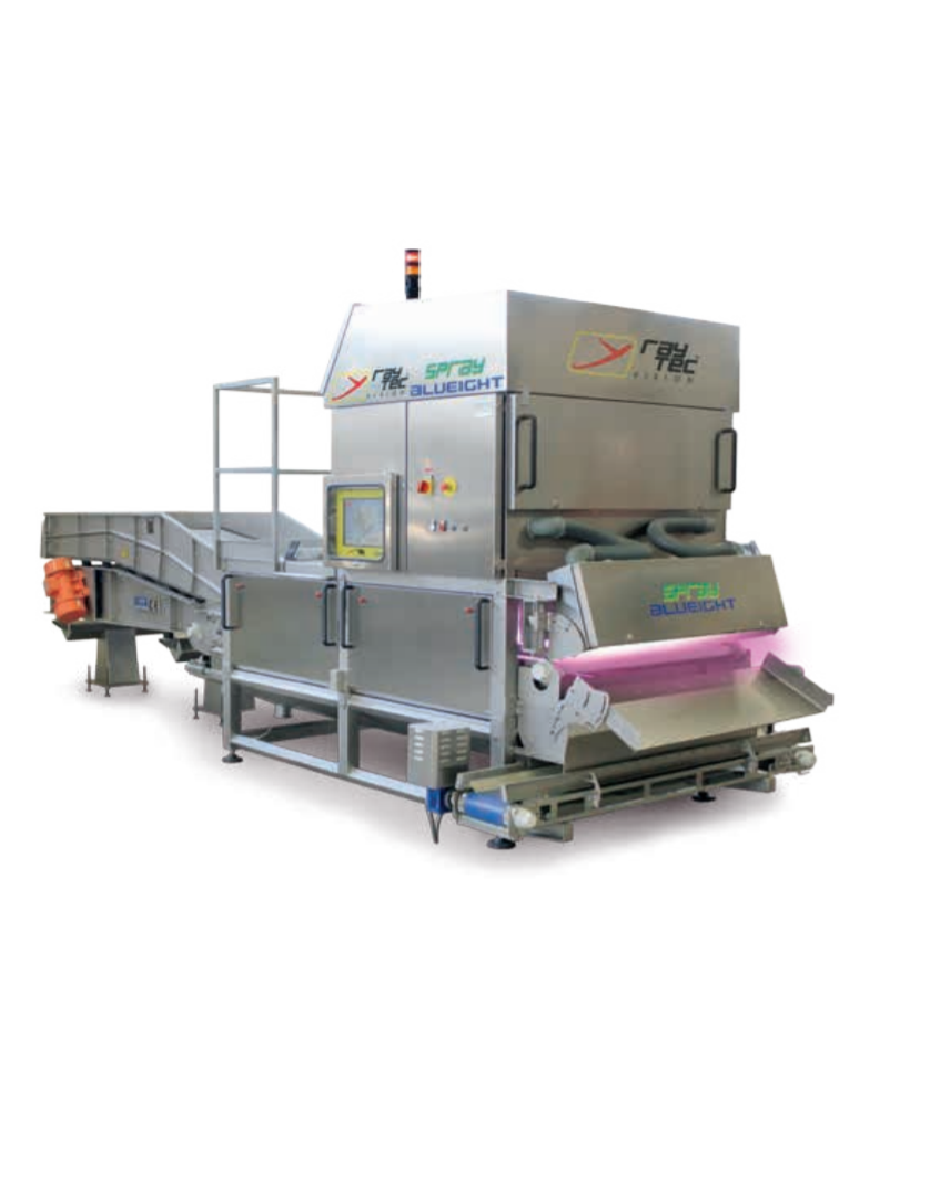
High resolution sorter for rejected colour defects, marked produce, and foreign bodies
The Spray Optical Sorter from Raytec is an optical sorting system that uses a high speed double vision system which can analyse 100% of the surface area of each item.
Spray is equipped with NIR (Near InfraRed) technology for Visible Colour analysis. This allows the machine to detect the presence of rot and foreign bodies of any colour, even black. It further allows colour defects to be detected, such as in under- or over-ripe products.
The system can be specified with an electro-pneumatic or air blast rejection system to suit your product requirements. Additionally, in “3 way” mode a second rejector can be fitted to allow for differentiation between unacceptable defects and those which are acceptable for second grade items, reducing waste.
Spray system is ruggedly constructed and designed for 3-shift continuous working. The belt speed is ranging from 60-150 m/min (197-492 ft/min) and the capacity varies per product.
Suitable for a wide range of fruit and vegetables including tomatoes, cherry tomatoes, potatoes, carrots, green beans, onions, peppers, artichokes, olives, apricots, cherries, oranges, apples, walnuts, peaches, strawberries, and pears.
Benefits
- Significant labour savings, up to 100% in some applications
- Designed to have low maintenance costs and 3-shift working capabilities
- High capacity options available, increase your throughput significantly
- 4x4mm pixel size for high accuracy and 100% surface coverage
- Rejection system options, including “3 way” for secondary gradings, reducing wastage