Saying goodbye to lumps in battery coating paste
Anything below a 50-micrometer speck of dust falls out of the visual acuity of the human eye. Yet, we can still perceive the effects of the things we cannot see.
The coating process for lithium-ion batteries is a case in point. The complex paste of binders, conductive agents, and active particles is coated a few micrometers thick on a conductor, but the presence of lumps can impair the batteries’ performance.
The critical process in achieving homogeneous coating slurry is mixing. However, mixing is never just mixing, as we’ve learned from Ralf Bürgelin, process expert at IKA Process Equipment. The most important factor is to get particles well dispersed and this can be accomplished by conducting the mixing process in-line.
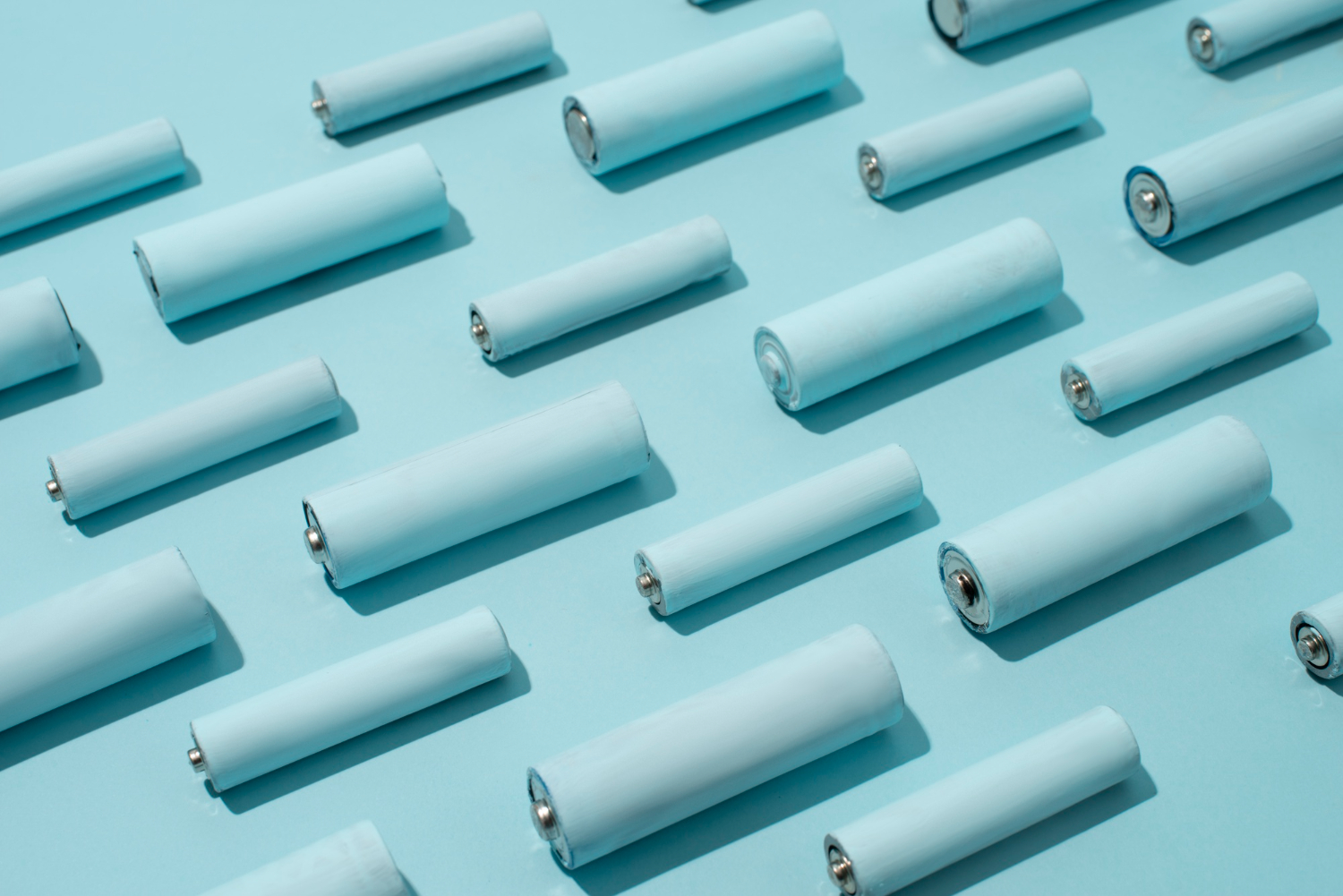
Increase energy to keep solids apart
“Ingredients like binders and carbon powders tend to agglomerate in liquid,” Ralf explains. These materials float on the surface and clump together as soon as they are introduced to a liquid phase.
Agglomerate formation is a problem for all slurry materials, but battery coating layers are applied at the micrometric scale, and imperfections are significantly amplified. Aggregates can vary in size, ranging from large to small. Big aggregates can result in scratches on the coating surface, while small aggregates can decrease the battery’s performance.
This is a main hurdle for conventional mixing to overcome. But IKA is no conventional technology provider: “We solve the challenge of agglomeration by conducting the dispersion inline within a small chamber in a high turbulence zone.” The intensity keeps the solid particles apart and distributes them uniformly throughout the liquid medium.
Reduce space in the mixing chamber to regulate particle motion
Besides energy, there is also the question of volume. When powders are released in large mixing vessels like planetary mixers, particles can escape. By contrast, IKA guides the liquid mixture in a small chamber where particles have no room to escape. This allows IKA to exert more precise control over the dispersal.
But doesn’t this high-energy mixing in a confined space generate excessive thermal stress on the materials?
“Temperatures should not rise over 50° C,” warns Ralf. In fact, the standard mixer from IKA operates at room temperature and rises to around 30-40 degrees as the mixture recirculates.
In line mixing, high turbulence, and a small chamber. These parameters are the levers that ensure a stable coating paste without agglomerates. Even though the active layer is smaller than a speck of dust, the quality of the lump-free coating is for all to see.