Reinventing Tradition in Butter Production
As consumer demands and regulatory requirements increase, the dairy industry faces significant challenges. FASA, a leader in butter processing and packing equipment, remains optimistic: “Despite these challenges, we foresee a robust future for dairy, particularly for traditional butter, which we believe will continue to flourish.” FASA is dedicated to supporting an evolving industry while staying true to its traditional roots.
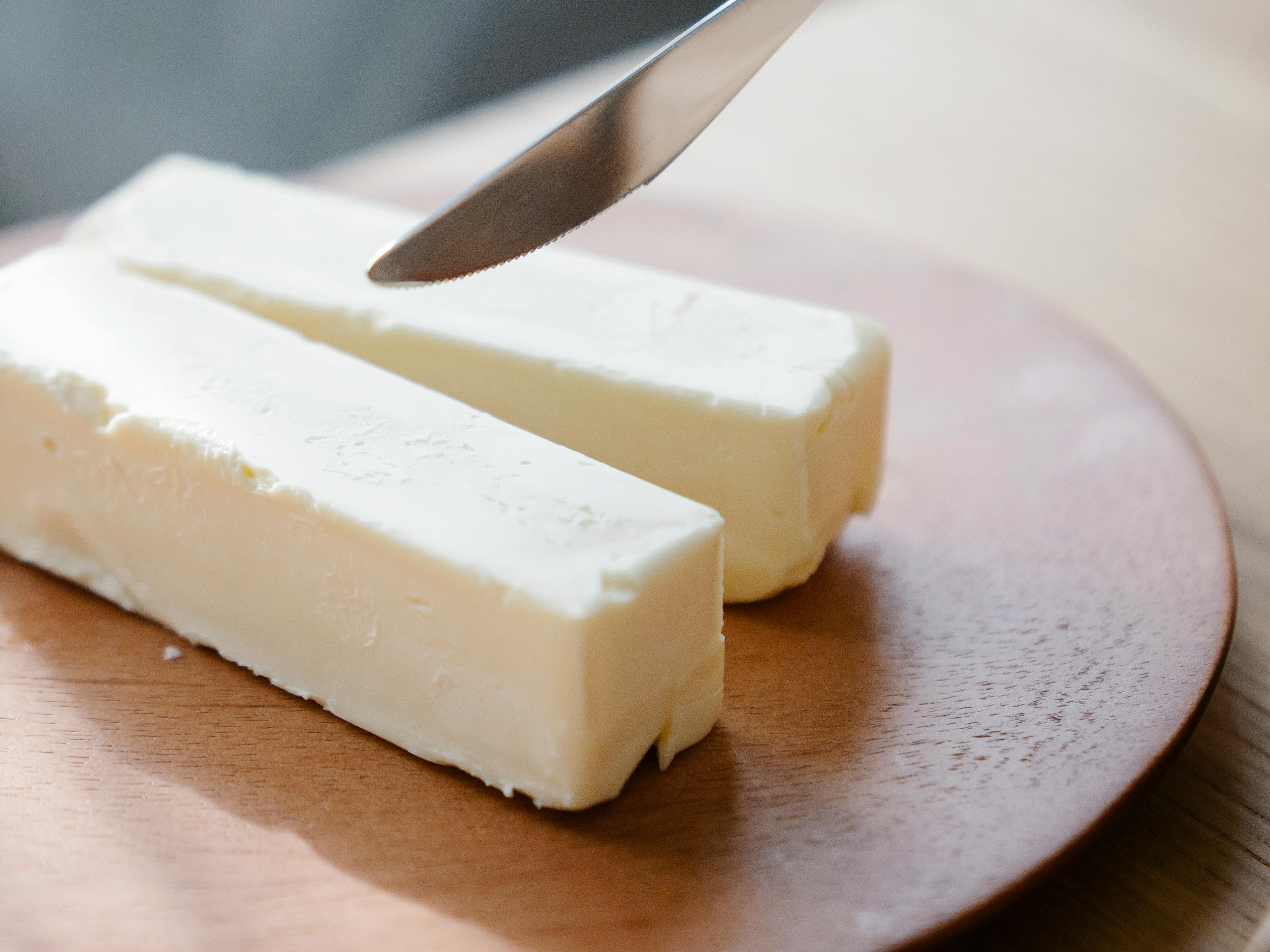
Enhancing Recipe Flexibility with the BMM Machine
FASA champions traditional 82% butter derived from both sweet and sour cream, offering versatility in production with their BMM machine. “Despite our eagerness to produce traditional butter, we also meet diverse customer needs by incorporating a variety of additives into churned butter, such as herbs, cocoa, salt crystals, and culture additives,” they explain.
Butter production is labor-intensive work, involving multiple skilled operators and significant resource input, which leads to inefficiencies and waste. “Our goal at FASA is to enhance these processes through sophisticated automation and improved Clean-In-Place (CIP) flexibility, ultimately reducing labor costs and minimizing waste,” explains the engineering team at FASA.
Redefining Industry Standards
Recently, FASA made significant strides in energy and water efficiency with their BMM, through the flexible adjustment of their CIP cyclogram. “This allows our clients to tailor the cleaning processes to their specific needs, enhancing waste management,” highlights the team. The full butter path is sandblasted to allow accumulation silicate film on the surfaces, for easy efficient cleaning.
The BMM stands out for its comprehensive approach to reducing waste and energy use. “Our BMM is designed in such a way that during melting operation all the melted fats would be pumped out to the auxiliary scope which then may be repurposed for production of other products when processed through fat recovery tanks.,” they assert. All components and parts of the BMM are crafted at FASA’s facilities. Every machine is assembled in-house before shipment to ensure flawless integration at the customer’s site. Additionally, FASA maintains strong client relationships through their 24/7 customer service and the availability of spare parts—each one produced in-house—to swiftly address any client needs.