Powder and liquid, a delicate equilibrium in paint production
Red, yellow, green, purple, blue… Paints and lacquers, a mix of pigments and possibilities, can bring colors to life and turn plain walls and surfaces into works of art.
Yet, achieving thorough dispersion and wetting of particles poses a challenge in paint formulations where powdered material can be 80% or more. And high viscosities, e.g., in wall paints, make it even more demanding to ensure uniform powder dispersion.
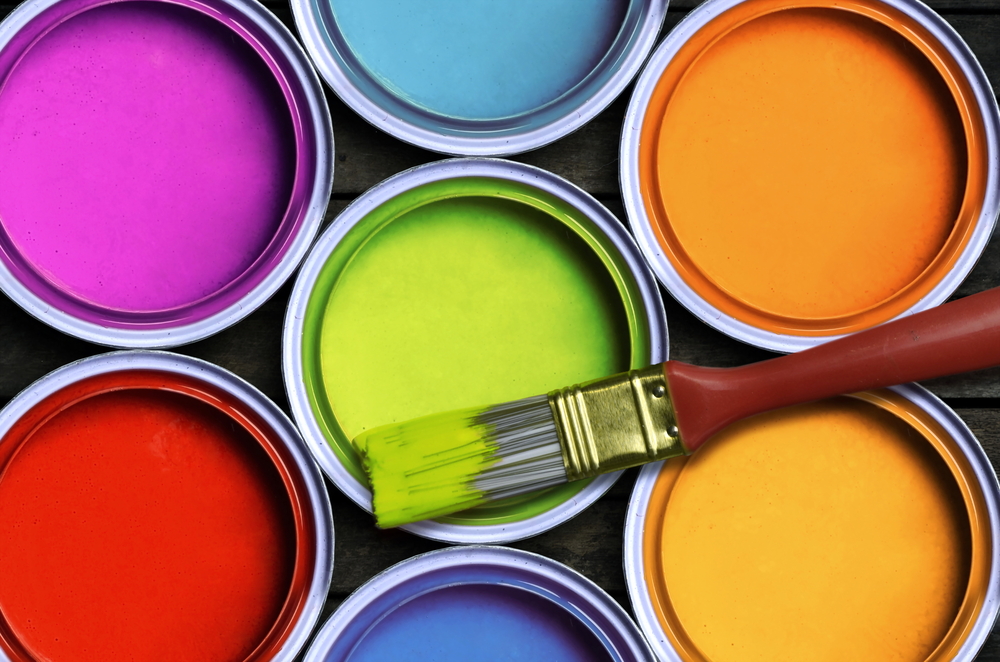
Today’s innovation is tomorrow’s tradition – the inline dispersing technology
In the traditional dissolver process, dry powder ingredients, such as pigments and solid additives, are poured into a big vessel with a liquid. The dissolver creates a strong vortex that draws the powder into the liquid. With this open process, powder particles often stick to the vessel wall, the agitator shaft, and the lid. This powder is missing in the mixture and there is always a risk that such adhesions will loosen in the course of the process and fall into the vessel as a solid agglomerate.
“Unlike conventional methods, inline powder-liquid mixers create a vacuum which is used to suck powder directly into the dispersion chamber where it hits the liquid in the high shear zone. This leads to a very fast complete wetting of the powder particles, and adhesions inside the vessel are eliminated,” explains Andreas Otte, Industry Expert at IKA.
Directly after powder incorporation, particle size distributions close to the primary grain are often achieved.
“In order to be able to reliably incorporate even challenging products like titanium dioxide, which has a very bad flow behavior and sticks to stainless steel, we use a versatile two-rotor-stator design. The first stage handles pumping and dispersing, ensuring a high flow rate for high-viscosity and high-powder-content products. The second stage is for liquid and powder dispersion to ensure precise powder particle distribution,” continues Andreas.
And when you mix powders with different properties, such as titanium dioxide and pyrogenic silica, this design flexibility allows the machine to be perfectly adapted to the product properties and requirements of the customer.
Don’t play with fire; instead, adhere to ATEX regulations
Flammable solvents in paints can evaporate and, when mixed with oxygen, create a fire or explosion risk. Therefore, compliance with ATEX gas and dust explosions regulations is vital to prevent such incidents.
“In the paint industry, various ATEX zones are present. There are Zones 0, 1, and 2 for gas explosions, with Zone 0 being the most critical – referring to vessels where an explosive atmosphere is continuously or frequently present,” adds Andreas.
Regarding dust explosions, ATEX has Zones 20, 21, and 22. Zone 20 is the most hazardous.
“IKA uses double-acting mechanical seals with temperature monitoring in the explosion-proof inline dispersion machines of the CMX type and, in conjunction with constructive safety, has achieved approval of the machines for ATEX Zone 0 and 20 (inside the machine),” concludes Andreas.
So, don’t play with fire, my friends. After all, we wouldn’t want our beautiful colors to turn into an unexpected fireworks show, would we?