Material discharge should be no burning issue for battery manufacturers
In 2023, the New York City Fire Department mounted a 200-firefighter operation to put out a massive residential blaze. It was only one of 130 fires in a year caused by a lithium-ion battery failure.
LIB devices catch fire when dendrite formation punctures the membrane separating the electrodes, shorting the circuit. The thermal pressures that develop from this excessive flow of current only need milliseconds to release the energy packed in the battery cells and explode.
If a battery containing a few grams of chemical solutions is enough to mutate a phone into a pocket bomb, handling the materials in bulk can turn a battery production facility into an inferno.
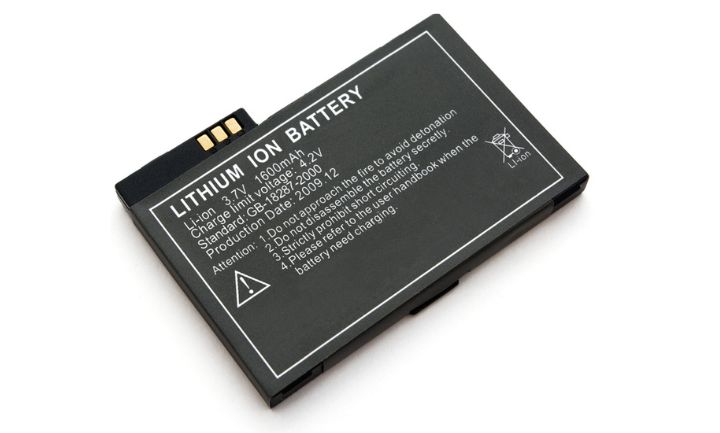
Exposure to impurities is playing with fire
The risks of combustion are especially high during the discharge process. Many of the production steps are performed in a contained environment, but the dispensing areas expose the materials to the elements.
If airborne particles and oxygen come into contact with the mixture, they destabilize the delicate chemical composition. Given the power density per batch, a small amount of impurities is enough to generate unforeseen reactions that could quickly burst into flames.
But in theory, such accidents are preventable. Handling materials in a closed system should keep them away from contamination.
It is Andocksysteme’s job to translate this theory into practice. The containment technology company is at the forefront of safe handling solutions.
A closed system is as strong as its high-containment valve
The risk profile of battery production mixtures hinges directly on the valve interface. In fact, discharge stations are the Achilles heel of a closed system and quality valves keep the process safe.
The perfect valve technology for battery manufacturers involves multiple layers of protection against contamination. The construction material is critical, which is why Andocksysteme builds its interfaces from inert stainless steel.
Another crucial factor is seal technology. With a reliable locking mechanism and tight-fitting seals the active-to-passive valves match together perfectly to avoid cross-contamination of these toxic fine powders. Moreover, the valve system must integrate into an automatic dispensing process typically deployed by manufacturers.
Seamless high-volume production is vital to an industry that is growing so fast. Indeed, the LIB manufacturing market is on fire. The right containment technology ensures that hazardous substances (powders) are transferred safely and operators are well protected.