Modular design for a fast fryer plant startup
Fast plant startups require well-defined roadmaps for scope, time, cost, and quality, to facilitate decision-making when purchasing and installing industrial technology. We spoke to Valeria Lucinschi, General Operations at Kuipers Food Processing Machinery, to learn how they ensure an efficient buying and installation cycle and align their fryers with producers’ goals.
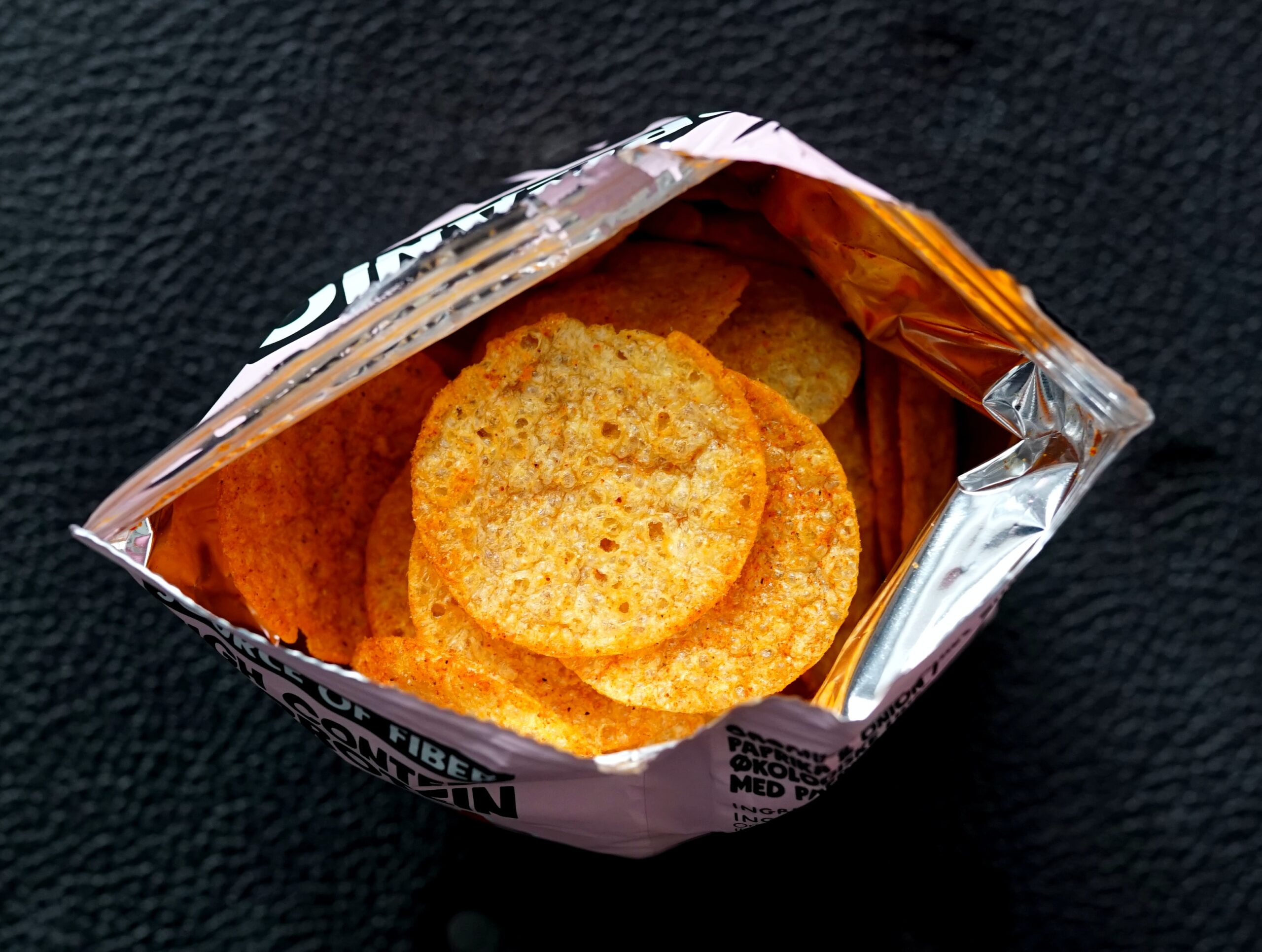
The buying cycle from product testing to FAT
Valeria explains that when you contact Kuipers to choose a frying technology for your snack, the food engineering team will observe the product’s behavior, document it, collect data, and perform computer simulations considering oil efficiency and turnover times. Product testing will help to determine the ideal fryer, size, oil amount, processing time, and other product-specific parameters. “Many new products need further testing to ensure the target outcome can be achieved,” Valeria states.
The buying cycle described by Valeria begins once the parameters are agreed upon. “The engineering department creates the drawings and sends a work order to manufacturing. When the fryer is built and assembled, Kuipers’ service team takes over with electrical pre-wiring and automation. Then the plant is fully pre-tested to ensure that all the main parts are functional. You are invited to attend the factory acceptance test (FAT) and may request alterations at this stage if needed,” Valeria indicates.
“After your agreement, the fryer is packed in Lego-like blocks and shipped. In the best-case scenario, a small standard fryer can be ready within 36 weeks. However, delivery times may be longer depending on the waiting list,” Valeria concludes.
Site preparation and modular design: the key to quick startup
Site preparation is crucial for a quick startup. Ensure your facility has the required electrical connection, automation cables, and piping in place beforehand. Kuipers’s modular design makes installation nearly plug-and-play. “The plant can be assembled like Lego blocks and plugged into the utilities,” Valeria says. Kuipers will run an acceptance test on your site and train your operators before finalizing the handover.
According to Valeria, “Kuipers’ modular design allows small standard frying plants to be operational within one week of delivery, compared to most equipment suppliers, which take about a month to install and start up a plant. This can save you a significant amount of time and money, considering that an average engineer day costs more than 1000 euros.”
When choosing industrial technology, consider the operation and maintenance requirements as well. Valeria highlights that “With Kuipers’ frying systems you can operate for many days without having to change your oil’’. These efficient systems allow you to produce continuously while not compromising your product quality.
Modular plant designs are a way to go if you want to start and run your production, saving time, and hence, money.