Grinding calcium carbonate down to size
We eat it; we wear it; we plaster it. But, most importantly, we grind it. Calcium carbonate is a pervasive material found in a raft of everyday products. Virtually all industries depend on it, either as a final or an intermediary product. But GCC is not all of a size, and a plurality of applications means different preparation requirements.
Ground calcium carbonate grains can be as coarse as 1,300 microns in poultry feed or as fine as 2 microns in paper coatings.
Milling the limestone to the correct particle size distribution is a test for GCC processing. But addressing this challenge successfully makes the difference between high and low-quality calcium carbonate materials.
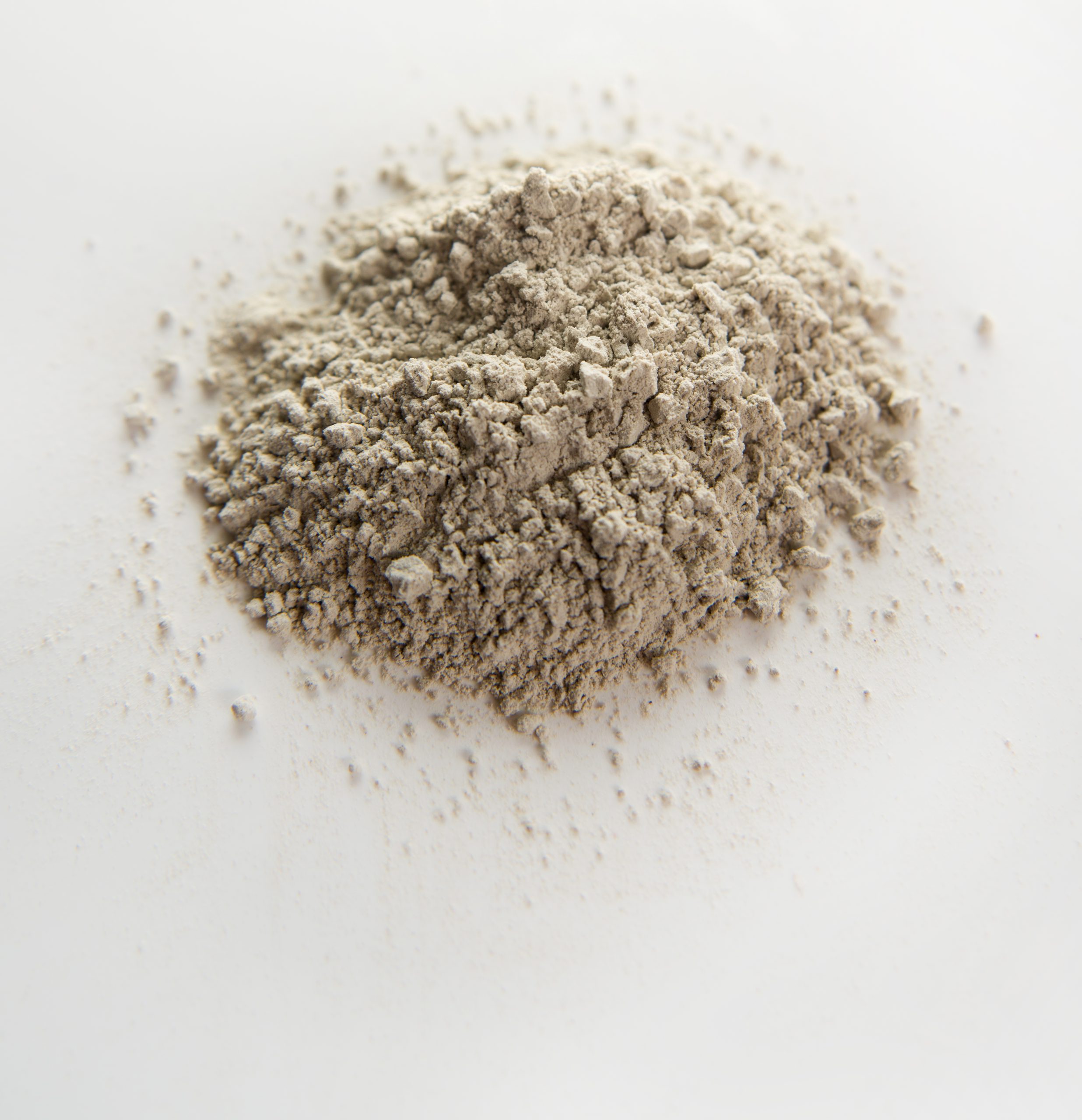
Mastering impact, shear, and attrition to control particle size
Crushed limestone is turned to powder in a spectacular engineering phenomenon that occurs at a millimetric level. Calcium carbonate particles are broken down through impact, shear, and attrition.
Imagine you shank to a nanoparticle and were dropped into a limestone-grinding mill. It would feel like a galactic clash. The blades in the equipment break the rocks by the force of impact; the swirling particles shear off against each other; large particles attrite smaller ones flying at different velocities.
But devising this intricate process to produce homogenous grains of accurate dimensions takes expertise with the raw material. Control over the impact, shear, and attrition parameters allows you to produce the right particle size distribution that matches multiple applications.
Find the right fineness profile for the job
Calcium carbonate is ubiquitous in manufacturing but producing it at a suitable grade demands precision and flexibility from the milling technology. Grinding is not simply a race to the finest grain size – equipment has to adapt to the specific use. The requirements change not only by industry but by manufacturer too.
Wood coatings, for example, typically use calcium carbonate as a filler. But manufacturers employ GCC of different grain sizes in their formulas, depending on the product range. Polymers made primarily to enhance the aesthetic effect of wood use GCC with a particle size distribution of around 7 µm. Coating products designed for scratch resistance require finer grains of about 3 µm.
Ground calcium carbonate is a versatile material, but its effectiveness is determined by the precision of particle dimensions. The power of GCC lies in its broad fineness spectrum, whether it is formulated into an antacid tablet, used to dye a silk shirt, or mixed to increase the adherence of wall paints.