Robotic loading systems for packaging applications
Enhance your production line with versatile robotic loading systems, designed to handle diverse products and optimize efficiency by seamlessly integrating into existing packaging workflows for precise and gentle handling across applications.
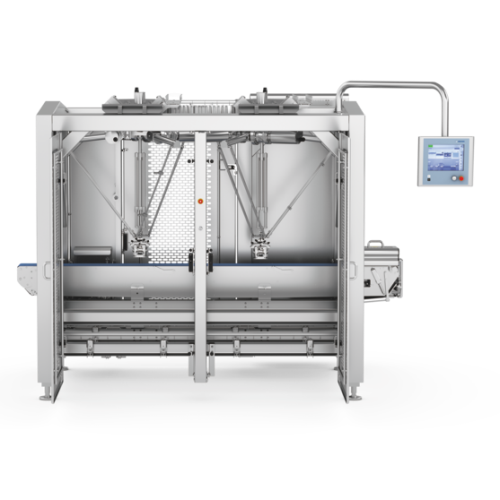
Automates Product Handling and Packaging Tasks
MULTIVAC, a leader in packaging solutions, offers advanced robotics that redefines efficiency in product handling and packaging. These versatile robots are engineered with servo drives and innovative gripper technologies, minimizing space usage and enhancing precision. Ideal for diverse industries such as food, pharmaceutical, medical, and consumer products, they accommodate applications from handling steak cuts to blister-packed pills.
The robots seamlessly integrate with both existing and new production lines, optimizing automation through modular designs that offer customizable options in robots, grippers, belts, sensors, and vision systems. The ability to retrofit existing systems ensures scalability and future-proofing. MULTIVAC robotics can operate continuously at high speed, maintaining low energy consumption and reducing the need for manual intervention, thereby decreasing operational costs and personnel requirements.
The equipment also boasts high hygiene standards, with easy-clean features to ensure maximum availability and compliance with industry regulations. By automating tasks such as product loading, converging, and pack removal, these robots boost throughput and flexibility across production lines. With support for integrated line control, MULTIVAC’s robotics provide seamless machine operation. Overall, they represent a future-ready solution in high-demand environments requiring precision and speed.
Benefits
- Enhances productivity by minimizing manual handling and increasing automation precision.
- Reduces operational costs through low energy consumption and optimized resource allocation.
- Maintains high hygiene standards with easy-to-clean designs, ensuring regulatory compliance.
- Adapts to changing production needs with modular and retrofittable options.
- Expands production capacity with seamless integration into existing lines, improving output and flexibility.
- Applications
- Sausage and meat products, Ready meals, Alternative proteins, Snacks, Cheese, Industrial and consumer products, Fish and seafood, Medical products, Vegetables, Poultry, Pastries, Pharmaceutical products, Fresh meat, Fruit
- End products
- Blister-packed pills, Salmon fillets, Chicken breasts, Diced peaches, Frozen lasagna, Plant-based burger patties, Ground beef patties, Potato chips, Sliced carrots, Steak cuts, Croissants, Sterilized syringes, Packaged screws, Boxed electronic components, Cheddar cheese blocks, Tofu blocks
- Steps before
- Product preparation, Material handling, Product inspection, Sorting
- Steps after
- Packaging, Inspection, Labelling, Box/container loading
- Input ingredients
- products, packs, boxes, containers
- Output ingredients
- thermoformed packs, trays, product packs, boxes, containers
- Market info
- Multivac is renowned for manufacturing innovative packaging solutions, specializing in vacuum packaging equipment, thermoformers, and labeling systems, catering mainly to the food, medical, and industrial sectors, with a strong reputation for quality and technological advancement.
- Automation
- High flexibility, Servo-driven, Modular
- Gripper Technology
- Innovative, customizable
- Integration Capability
- Direct integration into thermoforming machines
- Output
- Maximum efficiency, high output
- Precision
- High
- Space Requirement
- Minimum, compact design
- Retrofit Capabilities
- Extensible with additional degrees of freedom
- Hygiene Standard
- High, easy to clean design
- Energy Consumption
- Low
- Operating Costs
- Permanently low
- Pack Handling
- Automatic product loading and converging
- Loading Solution
- Automatic box/container loading
- Automation level
- Manual / PLC / SCADA
- CIP/SIP
- CIP 121°C / SIP 135°C
- Cleaning method
- CIP / Manual
- Energy efficiency
- 0.5–2 kWh/kg moisture
- Batch vs. continuous operation
- Batch / Inline Continuous
- Density/particle size
- 0.5–2.5 g/cm³ / 50–1000 µm
- Machine footprint
- Compact
- Gripper technology
- Servo-driven with various options
- Integration capability
- Directly into machine frame
- Robot types
- Linear, Parallel kinematics (2D/3D)
- Control panel type
- Touchscreen interface
- Control panel type
- Touchscreen HMI
- Integration possibilities
- Direct integration with thermoforming packaging machines
- Gripper technology
- Various grippers available
- Modular design
- Sensor and vision system customization
- Servo drives
- High efficiency