Softgel drying tunnel
Softgel capsules require a controlled secondary drying to reduce water content in the capsule to levels appropriate for product stability, further treatments including polishing, and final packing. After an initial run through a tumble dryer, the most effective way to finalise the drying process is by using a dedicated softgel drying tunnel. These ensure the capsules’ water content is reduced to the target levels with a gentle drying that preserves the quality of the capsule shell.
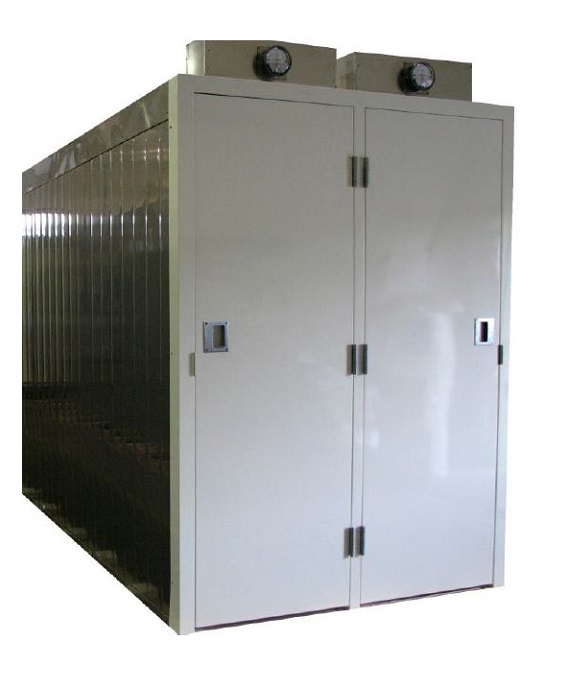
Dedicated soft gelatin capsule drying tunnels with innovative features
The LDT softgel drying tunnel from Technophar has been engineered to provide maximum performance while offering the benefits of simple on-site assembly. The LDT tunnel uses self-supporting wall modules made of 2 external walls of steel or plastic laminate, with a sealed internal styrofoam core. All materials used are Class 1 Fire Resistant and FDA/GMP approved.
This method of construction allows the tunnel to be shipped to your site in sub-assemblies that can be easily erected on your plant floor using the assembly equipment that is shipped with each tunnel. Technophar offers technical support and supervision for the final stage of installation, ensuring a top quality fit-out. The number of tunnels you need is determined by the output volume of the softgel encapsulation machine you have and the size and volume of capsules to be dried. A single tunnel unit is sized to accept up to 14 stacks of shallow drying trays.
LDT tunnels operate by using a contraflow of air to capsule path, with inlet air entering at the product exit, and routing to exhaust at the product entrance. This means moisture-carrying air hits the wet capsules, preventing the skinning that occurs when capsules meet fully dry air first. This promotes a gentle yet efficient drying as the capsules move through the tunnel from moist to dry air as they exit.
Benefits
- Lightweight, self-supporting wall modules for easy on-site assembly
- All surface treatments and tunnel components are fully FDA/GMP approved
- Manufacturer technical support and supervision of final installation to ensure quality
- “Moist air to dry air” path for capsules prevents skinning
- Customised design and build to suit your production volumes and plant room