Industrial piston compressors for various applications
Optimize your gas processing capabilities with versatile piston compressors, designed for efficient compression and regulation across a wide range of gasses, including hydrogen and biogas, ensuring seamless integration and reliable performance in demanding industrial operations.
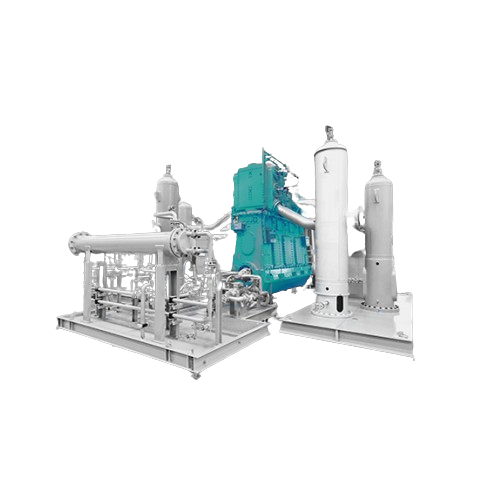
Regulates and Compresses Industrial Gases
Neuman & Esser’s industrial piston compressors excel in gas compression across diverse sectors. These compressors utilize a robust multi-stage technology, ensuring precise regulation and high-pressure performance for applications like hydrogen and biogas processing. Capable of managing up to 100,000 Nm³/h, they integrate seamlessly into existing setups with options for oil-free or lubricated designs. Energy efficiency is enhanced through variable-speed motor optimization, reducing consumption by up to 30%. Constructed from corrosion-resistant materials, they meet rigorous compliance standards, including API 618, for safe operation in demanding environments. Customization is available, supported by expert engineering for tailored solutions.
Benefits
- Enhances operational efficiency with multi-stage compression for precise gas handling.
- Reduces energy costs by up to 30% with optimized motor control.
- Provides flexibility with customizable configurations for diverse industrial applications.
- Minimizes maintenance through corrosion-resistant materials, ensuring long-term reliability.
- Ensures compliance with API 618 standards, promoting safety in high-pressure environments.
- Applications
- Oil and gas industry, Recycled resources, Raw materials, Carbon black, Green gas industry, Battery storage systems, Natural gas, Biogas, Chemical industry, Hydrogen production, Food and beverage industry, Hydrogen, Industrial gas processing, Powder coating, Protein enrichment
- End products
- Carbon black products, Beverages, Hydrogen electrolyzers, Ammonia, Helium, Ground raw materials, Refined petroleum products, Synthetic natural gas, Powder coated metals, Compressed hydrogen, Biogas fuel, Processed food items, Recycled plastic pellets, Fortified protein powders, Soda ash, High-performance batteries, Lng (liquefied natural gas)
- Steps before
- Site evaluation, Feasibility assessment, Financing, Engineering, Construction
- Steps after
- Commissioning, Trading of gases, Maintenance, Upgrading, Modernization
- Input ingredients
- hydrogen, mixed gases, hydrocarbon gases, corrosive gases, toxic gases, CO2, biogas, oxygen, gases with abrasive particles, highly flammable gases
- Output ingredients
- compressed gases, technical gases, natural gas
- Market info
- Neuman & Esser Group is known for its expertise in manufacturing compressors and grinding systems. They hold a strong reputation for providing durable, high-quality engineered-to-order equipment, particularly in the oil and gas, chemical, and energy industries.
- Suction Pressure
- Adjustable
- Discharge Pressure
- Max. 15, 000 psi
- Power Range
- Max. 41, 000 hp
- Flow Rate
- Max. 60, 000 scfm
- Number of Cranks
- 1, 2, 4, 6, 8
- Number of Stages
- 1 to 8
- Speed
- Max. 1, 200 rpm
- Lubrication Design
- Oil-free or Lubricated
- Cylinder Cooling
- Water-cooled
- Drive Type
- Natural Gas, Diesel, Electric
- Operating Design
- Flexible Labyrinth System
- Application Type
- Dry-running
- Energy efficiency
- High
- Automation level
- Manual / PLC / SCADA
- Adjustable volume flow rates
- Yes
- Flexibility to process changes
- High
- Discharge pressure
- Max. 15, 000 psi
- Flow rates
- Max. 30, 000 scfm
- Power range
- Max. 41, 000 hp
- Oil-free or lubricated design
- Available
- Ease of maintenance
- Short maintenance time
- Operational adjustability
- Flexible capacity or volume flow
- Cooling options
- Water-cooled or air-cooled
- Design standards
- API 618 compliant
- Noise level
- Quiet operation
- Foundation load
- Low
- Sealing system
- Flex Labyrinth
- Density/particle size
- 0.5–2.5 g/cm³ / 50–1000 µm
- Application gases
- Hydrogen, mixed gases, hydrocarbons, CO2, biogas, oxygen
- Machine footprint
- Vertical / V-Type / Horizontal
- Design orientation
- Vertical / Horizontal / V-Type
- Control panel type
- Customizable
- Discharge method
- Configurable based on application
- Number of cranks
- 1, 2, 3, 4, 6, 8
- Number of stages
- 1 to 8
- Design Type
- Oil-free / Lubricated
- Compressor Type
- Vertical / V-Type / Horizontal
- Number of Cranks
- 1, 2, 3, 4, 6, 8
- Number of Stages
- 1 to 8
- Cooling Method
- Water-cooled / Air-cooled
- Drive Options
- Natural gas / Diesel / Electric
- Sealing System
- Contact / Non-contact (Flex Labyrinth)
- Application Type
- Standard / High-Speed