Don’t let your biogas waste go to waste! Turn it into fertilizer, recovering up to 80% of your energy
Digestate is a byproduct of biogas production. As bacteria break down organic matter to produce biogas, any remaining solids and liquids that aren’t converted into gas are known as digestate.
But if you think all digestate is created equal, think again my friends!
Digestate can be sourced from either sewage sludges or food waste. While the former may contain heavy metals such as cadmium or nickel, which can pose a health risk if introduced into the food chain, the latter produces a cleaner and purer digestate that is ideal for use as fertilizer.
How can you turn digestate into fertilizer? Better yet, how do you do it in an energy-efficient and clean way?
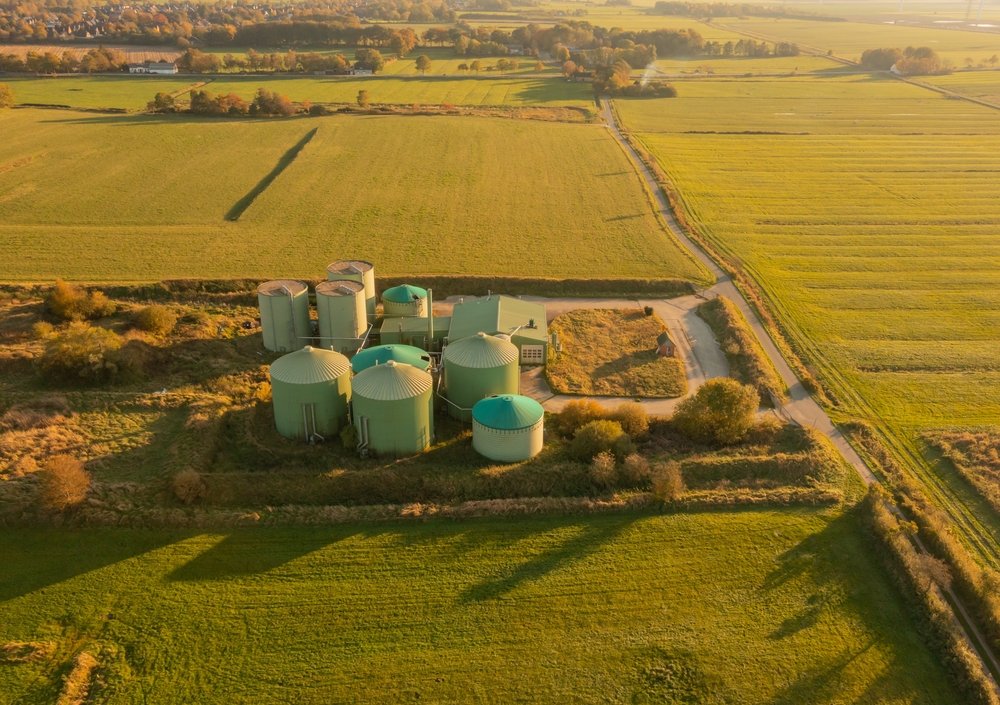
The way to go green is by using steam drying technology
We had the chance to speak with Prem Verma from Swedish Exergy, specialized in steam drying technology with a focus on energy efficiency.
The digestate that comes out of the biogas production has a very high water content of around 95%. Therefore, it first needs to be mechanically pressed to reduce the moisture content to 80%, followed by drying.
“In contrast to conventional methods that rely on hot air or gas for drying, we are drying or dewatering the digestate in an inert atmosphere, i.e., we are using the moisture of the digestate itself as a drying media,” explains Prem.
In an open drying system, a significant amount of ammonia is generated and will escape into the atmosphere. Swedish Exergy’s steam drying method is carried out in a closed and controlled system that makes sure no emission or smell is released into the environment.
“In our steam dryer, ammonia is collected as low-pressure steam that is then condensed. The resulting liquid ammonia can be recovered and used as liquid fertilizer or further processed and dried to produce solid ammonium sulfate, a nitrogen-rich fertilizer,” continues Prem.
“Now, let’s talk about stack losses…” Stack what?
Stack losses refer to the loss of energy and materials during industrial processes, leading to greenhouse gas emissions that can contribute to climate change.
“Open-air dryers require outdoor air to be heated up to 90/100°C in order to dry the product. The hot air is then released into the environment at 50/60°C, resulting in energy loss and the discharge of heat and moisture into the atmosphere,” adds Prem.
By continuously recirculating the drying air in the closed system, the steam dryer can capture and recover most of the heat in order to reduce energy losses and emissions.
“We only need the energy to heat the water, about 750 kW per ton, with around 600 kW (80%) of it recoverable as low-pressure steam. As a result, our process only consumes 150 kW/hr per ton of water, just 15% of the energy required by conventional dryers,” concludes Prem.
Steam drying takes fertilizer production to the next level. It cuts emissions, enhances handling, preserves nutrients, and consumes just 0.15 the energy of traditional drying methods—a win-win for production and the environment.